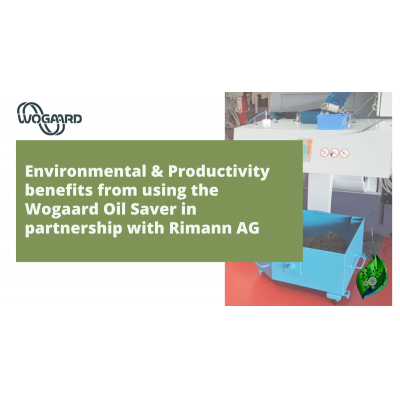
Rimann Oil saver
Rimann AG has worked for many years for the company Neida Bartschi AG and had supplied them one of there ARYMA 51-2 chip spinners to separate the neat oil from the chips to ensure the swarf was less than 3% moisture dry along with re-using the oil.
Neida Bartschi AG had recently upgraded all the sliding head machines to increase productivity however were using old chip bins/trolleys from the older machines.
The Mayfran conveyor also dragged a lot of oil in the chip trolleys so the machines would stop at night because there was not enough oil in the machine tank causing a number of hours of lost production.
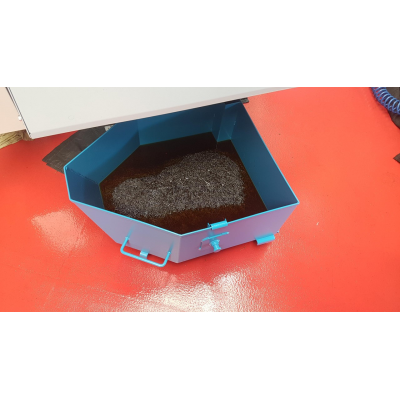
Bin Full Oil
BEFORE
Additional issues when tilting/emptying the swarf from the full chip trolleys in the ARYMA Chip spinner was the high amount of oil flushing in and out of the centrifuge causing a big mess!
Much of the work Neida Bartschi AG manufactures are for the medical industry so no oil mixing is allowed between machines. Even after spinning the swarf/chips the drained oil could not be re-used on these machines resulting in higher oil costs and usage.
The old chip trolleys were not long enough for the Mayfran conveyor so, oil and chips dropped on the floor causing Health and safety issues.
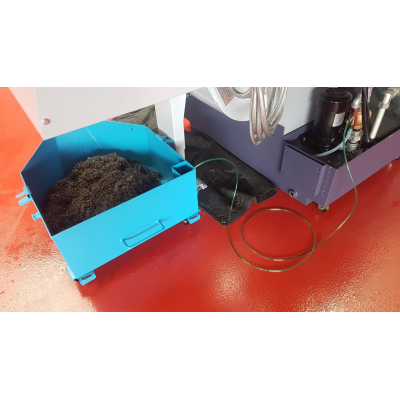
Empty Bin with Oil Saver
AFTER
Rimann AG solution was to introduce the Wogaard oil saver and ARYMAchiptrolleys!
The Wogaard oil saver unit is connected to the machine's pump and reclaims the fresh oil as soon as it drops into the chip bin and takes it back to the machine tank. As it is connected to the machine pump it works automatically when the machine is in operation so no additional manpower. Wogaard also does a similar device for soluble coolant.
The results of the project are the oil is now going back into the same machine, a much cleaner environment and a happy customer which found a good and simple solution.