Rimann AG a leading supplier in filtration, separation and chip separation devices with a focus on environmental recycling and reusing in the metalworking industry.
The latest project involved supplying the Oil saver manufactured by Wogaard and new chip bins to Neida Bartschi AG in Switzerland
View Article
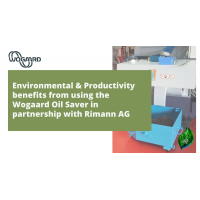