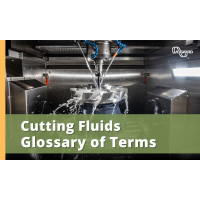
Fluidi per il taglio dei metalli - Glossario dei termini
Fluidi per il taglio dei metalli - Termini del glossario Le seguenti serie di pubblicazioni hanno lo scopo di fornire ulteriori informazioni sul mondo dei fluidi per il taglio dei metalli per aiutare tutte le persone coinvolte nell'uso dei fluidi da taglio a prendere le misure necessarie quando si tratta di questi prodotti, sfruttandoli al massimo in termini di riduzione. , riutilizzo e riciclaggio. Di seguito, ti presentiamo un glossario di termini che siamo certi sarà molto utile.
Visualizza articolo