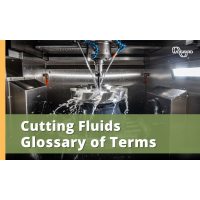
Sorry there was a problem!
Article not found!
Wogaard Ltd Article
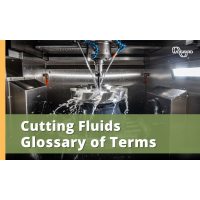
Metal Cutting Fluids - Glossary Terms
The following series of publications are intended to provide further information around the world of metal cutting fluids to help everyone involved in the use of cutting fluids to take the necessary measures when dealing with these products while making the most out of them in terms of reducing, reusing and recycling. Below, we present you a glossary of terms that we are certain it's going to be very useful.
View Article
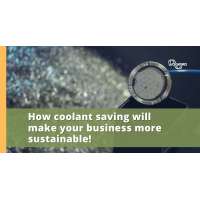
How Coolant Saving will make your business more Sustainable!
How coolant saving will make your business more Sustainable!
Hi, I am Jason Hutt from Wogaard limited, who provide oil and coolant saving solutions. Sustainability is a focus for Wogaard and I would like to run through one of the areas highlighted on a previous blog about achieving sustainability goals in manufacturing in bite sized steps.
View Article
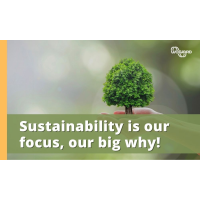
Sustainability is our Focus, our big Why!
Sustainability is our Focus, our big WHY!
Hi, I am Jason Hutt from Wogaard limited. We supply coolant and oil saving solutions to the manufacturing industry. And I would like to talk about Wogaard’s focus on Sustainability.
View Article
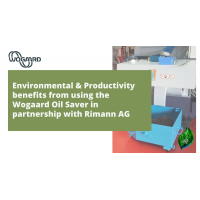
Rimann AG - Environmental and productivity benefits from using the Wogaard Oil Saver
Rimann AG a leading supplier in filtration, separation and chip separation devices with a focus on environmental recycling and reusing in the metalworking industry.
The latest project involved supplying the Oil saver manufactured by Wogaard and new chip bins to Neida Bartschi AG in Switzerland
View Article

Wogaard showcasing coolant-saving innovation at GTMA Manufacturing Solutions Ireland 2019
GTMA Manufacturing Solutions Ireland 2019
Wogaard will be demonstrating their award-winning Coolant Saver technology at the popular event that will be taken part at the Limerick Institute of Technology next 12th Jun.
View Article
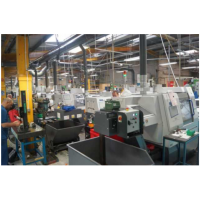
Wogaard Oil Saver supports Roscomac’s family values
Wogaard Oil Saver supports Roscomac’s family values
When Worthing-based Roscomac was established by Fernando Martello in 1976, the subcontract engineering business was founded on strong family values. During the following years the business has done its utmost tomaintain a ‘family’ environment, both within the company and embodied in its staff and its approach to customers. Today, the Wogaard Oil Saver is helping to support these key values.
View Article
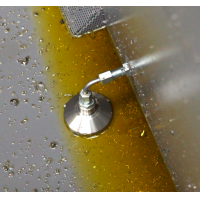
Innovation meets Application - Wogaard Coolant Saver at Renishaw
Innovation meets Application - Woogard Coolant Saver at Renishaw
Renishaw is one of the world's leading engineering and scientific technology companies, with an enviable reputation in precision measurement and healthcare equipment. The company supplies products and services used in applications as diverse as aero engine and wind turbine manufacture, through to dentistry and brain surgery. At its Stonehouse UK machining facility the Award-winning Wogaard Coolant Saver is running around-the-clock,recovering the neat oil coolant used on each of Renishaw’s CNC slidingheadstock lathes.
View Article
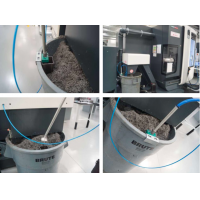
Wogaard Coolant Saver takes off at Progressive Technology
Wogaard Coolant Saver takes off at Progressive Technology
Progressive Technology has always been an early adopter when it comes to equipment that can benefit the performance of the business, the Wogaard coolant saver. One of the company’s latest benefits has come from a simple, but effective, method of reclaiming the coolant from the swarf bins located alongside each of its advanced machine tools using the Award-winning Wogaard Coolant Saver.
View Article
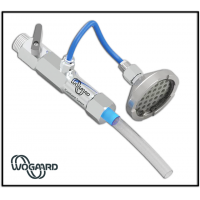
7 tips to install Wogaard's Coolant Saver
7 tips to install Wogaard's Coolant Saver
Follow these 7 tips to install Wogaard's Coolant Saver. Installation time is between 30 and 60 minutes in majority of cases.
View Article
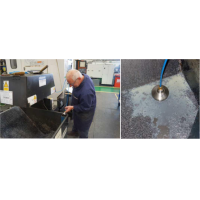
Coolant Saver Technology provides a plate full of benefits - Cook Compression
Coolant Saver Technology provides a plate full of benefits - Cook Compression
Part of the multinational Dover Corporation, Cook Compression has seen a number of benefits following the installation of award-winning Wogaard coolant saver units on its CNC machine tools. Unusually, the cost-effective unit proved its worth on a band saw before being installed across the shopfloor.
View Article