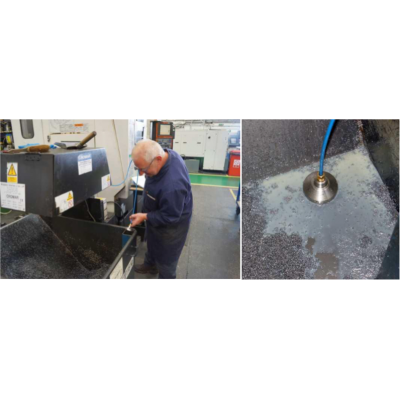
The Wogaard coolant saver has been saving Cook Compression time and money.
The Dover Corporation is one of the largest global engineering companies; it is comprised of over 500 companies turning over a total of around $8 billion per year. As a strategic part of the multinational Dover Corporation, Cook Compression Group provides solutions for the global reciprocating compressor market. From its facilities in Ellesmere Port, Cook Compression supports customers in the energy sector and is the group’s Centre of Excellence for plate valves.
Used in industrial double-action reciprocating compressors, plate valves act as spring-loaded non-return valves. The double acting piston creates suction and discharge and the differential change in pressure will shut the suction valve and open the discharge to allow the gas to move. These sophisticated compressors are used by companies requiring efficient gas transfer, such as major oil and gas refineries.
Compressors of this type must offer longevity in the field so the plate valve material must be correctly specified and accurately manufactured. That said, Cook Compression also provide refurbishment and upgrade support for its customers.
Plant Manager, David Wain, says: “The main material for valves is 416 stainless, but we also machine 420 stainless, 17/4PH, 300 series stainless as well as cast irons. Valve Internals are made from 420 stainless and engineering plastics, such as PTFE, PEEK and Nylon. Depending on what the customer is compressing different materials will be specified so that the gasses do not attack and corrode the valve plate material. We put a lot of effort into the R&D of new materials to improve the performance of compressing different types of gas. Some of the compressors run dry while others are lubricated , this affects the valve material choice for differentapplications.”
To manufacture its products the company operates a significant number of CNC machine tools on site, with key machines running around-the-clock. “Cook has grown by around 15 per cent year on year over the last 10 years, so we have been investing in new manufacturing technology, making the whole facility more efficient,”explains David Wain.
He continues: “Including the two new Doosan machines tools recently installed, wehave 17 CNC machines on site, which vary from 2-axis CNC lathes to multi-axis lathes and machining centres. We also have a Kasto Twin A2 CNC band saw capable of cutting material up to 300mm diameter.
“The saw is a very reliable piece of kit. However, it was consuming a significantamount of coolant due to the small chips dragging it out on the swarf conveyor. We had seen the Wogaard coolant vacuum tool when Business Manager, Jason Hutt, came to explain the benefits of it to us. He allowed us to have one on trial, although there was no previous case of the unit being used on a CNC saw. The only question mark was the size of the pump, but we gave it a try and it has really paid dividends.”
Prior to installing the coolant saver the saw operator, Matt Hollins, would have to use a drain tap to remove any coolant from the swarf bin, using a 5 litre drum to catch it and pore the coolant back into the tank, hopefully without spilling too much on the floor. As the drain hole was about 6mm off the bottom of the bin there is always a residue left in the bin so it was not an ideal method.
Connected to the coolant pump by a flexible line, the coolant saver is simply placed in the saw’s swarf bin. When the machine is running the coolant pump is used togenerate a vacuum by the Wogaard unit, which simply draws the coolant back up from the bin and back into the machine’s tank. “With the coolant saver fitted the bins are now practically empty when we check them,” Matt Hollins says. “We were topping up the tank with 25 litres once a day, this has been reduced to once a week, or a maximum of twice a week if it is running on more than two shifts.”
Such was the success of the coolant recycling kit on the band saw that the company decided to fit a Wogaard unit to each of its machine tools. One of the first to be fitted was a Mazak Nexus vertical CNC machining centre, as machine operator, Joe Diggery, recalls: “We were topping that machine’s tank up once a day with around 50 litres, and now it is just two or maximum three times per week.”
Dry swarf has another benefit to the business, as HSHEQ (Health and Safety,Hygiene, Environment and Quality) Manager, Phil Avis, explains: “The swarf bins get emptied twice a day if the machines are running flat out. The swarf is collected by a recycling company and whatever coolant was left in the bins had to be poured into IBCs for correct disposal. This of course incurred an additional cost.”
Although the company is still monitoring the savings achieved with the coolant saver, a rough calculation shows a saving of around one barrel of coolant per month, which gives a payback of less than 6 months.
Phil Avis concludes: “Installation is simple, especially after you have done one.Since we have had them fitted, not only are the operators happy with the results, but it will also have a major impact on our environment, especially as we pursue ISO 14001 accreditation. We want to get everything in place before we call the auditors in, and with this project allowing dragged out coolant to be effectively pumpedstraight back into the machines, it is a win:win situation.”