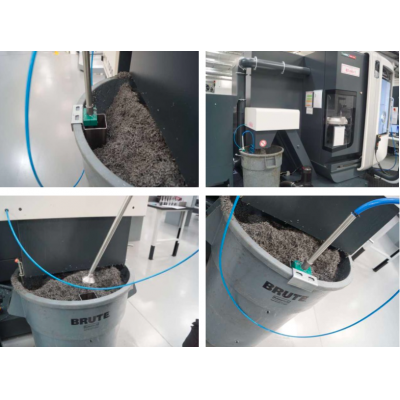
L' économiseur de liquide de refroidissement Wogaard utilisé par Progressive Technology.
En fournissant des services d’usinage avancés à commande numérique pour la plupart des secteurs de pointe de l’industrie de haute technologie, Progressive Technology, basée à Newbury, a considérablement changé de méthodes et de capacités par rapport au point de départ des activités de la société. Cependant, sur le plan géographique, l'activité n'a pratiquement pas bougé, l'entreprise familiale ayant été initialement créée à Overton, juste à l'extérieur de Basingstoke, à moins de 30 minutes. Lorsque le propriétaire de la société a repris la petite entreprise de fabrication de gabarits et d'outils de son père en 1995, il a investi dans la technologie d'usinage EDM et CNC pour répondre aux besoins de ses clients.
Puis, il y a environ 7 ans, la société a investi dans la technologie d'usinage 5 axes à commande numérique lorsqu'un fournisseur de composants de formule 1 basé à Newbury a décidé de suspendre ses outils. «Nous avons acquis le bâtiment et une partie des équipements de la machine-outil», se souvient Ashley Mizen, ingénieur en améliorations. «Bien que nous n’ayons pas repris les affaires. Les clients du sport automobile se sont tournés vers nous pour combler le vide laissé. Nous avions l'équipement et la capacité, alors nous avons appliqué nos connaissances en ingénierie aux différents projets et les progrès ont ensuite été réalisés.
«À l'époque, nous avions le site 5 axes à Newbury, ainsi que les fraiseuses de tournage et de fraisage vertical à Overton. Nous avons continué à progresser et avons transféré toutes les opérations de fraisage sur le site d'origine de Newbury. Avec l'achat de plus de machines, nous sommes sur le point d'exploser. Nous avons donc commencé à chercher d'autres sites à Newbury, puis nous avons acheté notre installation actuelle il y a environ trois ans. »
Après un vaste programme de rénovation, l'unité de 5 000 m2 était prête à être occupée, mais la fenêtre d'opportunité pour se déplacer entre les périodes de pointe de la saison de sport automobile n'était que de deux semaines. «Nous avons déplacé les machines-outils que nous gardions et en avons remplacé d'autres. Notre ancien Mikron a été mis à jour avec un nouveau Mikron HPM600U. Deux nouveaux DMG 40 eVos ainsi que deux nouveaux DMG 60 eVos ont également été ajoutés à la liste des installations », déclare Ashley Mizen.
Cette philosophie d'investissement s'est poursuivie au fur et à mesure que l'entreprise grandissait, avec l'ajout de trois centres d'usinage de motifs CMS à 5 axes, de deux nouveaux centres d'usinage Hedelius à 5 axes et d'un DMG DMU 50. Il poursuit: «Nous sommes une entreprise de réaction rapide; nous avons un carnet de commandes qui fluctue beaucoup. En travaillant avec toutes les équipes majeures de la F1, nous investissons constamment dans les nouvelles technologies. Nous spécifions nos machines avec beaucoup de précision, avec de nombreuses fonctionnalités supplémentaires incluses pour les rendre aussi efficaces et polyvalentes que possible. ”
Aujourd'hui, la main-d'œuvre hautement qualifiée de 60 personnes travaille 7 jours sur 7, 24 heures sur 24. Les matériaux coupés comprennent une gamme complète de plastiques techniques, d'aciers inoxydables, d'aciers à outils traités thermiquement, d'aluminium de la série 7, de titane et d'alliages résistant à la chaleur tels qu'Inconel, ainsi que de composites à matrice métallique à inclusions de silicium utilisant des outils PCD. Ashley Mizen a déclaré: «Tout est question de s'assurer que les bons emplois sont confiés au bon ingénieur.»
La taille des lots varie, les clients du sport automobile peuvent commander 12 pièces; six de chaque main, alors que les composants médicaux de précision sont normalement à 500 pièces. «L'un des problèmes les plus importants pour nous est que nous utilisons une grande quantité de fluide de refroidissement à broche à haute pression, de sorte que les machines ont tendance à être inondées à moins que les convoyeurs de copeaux ne restent allumés en permanence. Cependant, cela remplit rapidement les bacs à copeaux avec du liquide de refroidissement. "
«Lorsque les règles relatives à la ferraille ont été modifiées récemment, nous avons décidé de faire appel à un fournisseur de services unique, mais ils ne voulaient pas prendre nos déchets à l'état humide. Nous avions un système en vertu duquel les bacs à copeaux étaient chargés sur un appareil, puis basculés pour s'égoutter. C'était un processus compliqué et très inefficace. Il a été effectué à l’intérieur par quelques personnes et il était impossible de drainer les copeaux proprement. Cela risquait également de provoquer un risque en cas de déversement de liquide de refroidissement sur le sol de l'atelier. Nous avons également engagé une personne chargée de la maintenance à plein temps pour reconstituer le liquide de refroidissement dans les puisards des machines-outils », explique Ashley Mizen.
Le directeur des ventes, Jason Hutt, a présenté le système de recyclage des liquides de refroidissement Wogaard à la société: «Tout le monde chez Progressive Technology pouvait voir les avantages de l’installation de l’économiseur de liquide de refroidissement, mais la charge de travail rendait difficile l’équipement des unités sur les machines. . Il ne leur faut que 20 minutes environ pour s’adapter, mais le calendrier était si serré que même une si petite pause était introuvable. ”
Ashley Mizen ajoute: «Nous avons arrêté une machine choisie pour intégrer l'économiseur de liquide de refroidissement lorsque nous avons identifié un problème de liquide de refroidissement dans la poubelle pour un travail particulier. Nous ne savions pas combien de temps il allait falloir installer, nous étions donc réticents à arrêter une machine pendant notre période de pointe. Nous avons constaté que l'installation de l'unité d'essai initiale sur la machine ne prenait vraiment pas de temps, mais la modification de nos bacs à copeaux pour l'adapter à l'économiseur de liquide de refroidissement était un processus fastidieux. Nous avons testé la première unité pendant quelques semaines et nous en avons immédiatement constaté les avantages, elle est simple à utiliser et, avec notre mélange de liquide de refroidissement miscible à l’eau fonctionnant entre 6 et 9%, nous avons évidemment économisé une fortune, avec les avantages suivants: de remblais de puisard et d’amélioration de l’entretien ménager. "
En plus d’un économiseur de liquide de refroidissement spécialement conçu pour les tours CNC à tête coulissante de style suisse, Wogaard développe également un module de copeaux à copeaux qui rendra l’installation du système beaucoup plus efficace.
Jason Hutt conclut: «Nous savons que les entreprises très actives telles que Progressive Technology auront toujours du mal à trouver le temps de s'adapter à nos unités d'économie de liquide de refroidissement. Nous concevons donc du matériel auxiliaire de manière à le rendre aussi rapide et simple que possible. En plus du module de copeaux, nous proposerons également des kits de raccords sur mesure. Ainsi, si nécessaire, tous les raccords de tuyauterie nécessaires pour une machine-outil spécifique seront fournis avec l' économiseur de liquide de refroidissement. ”